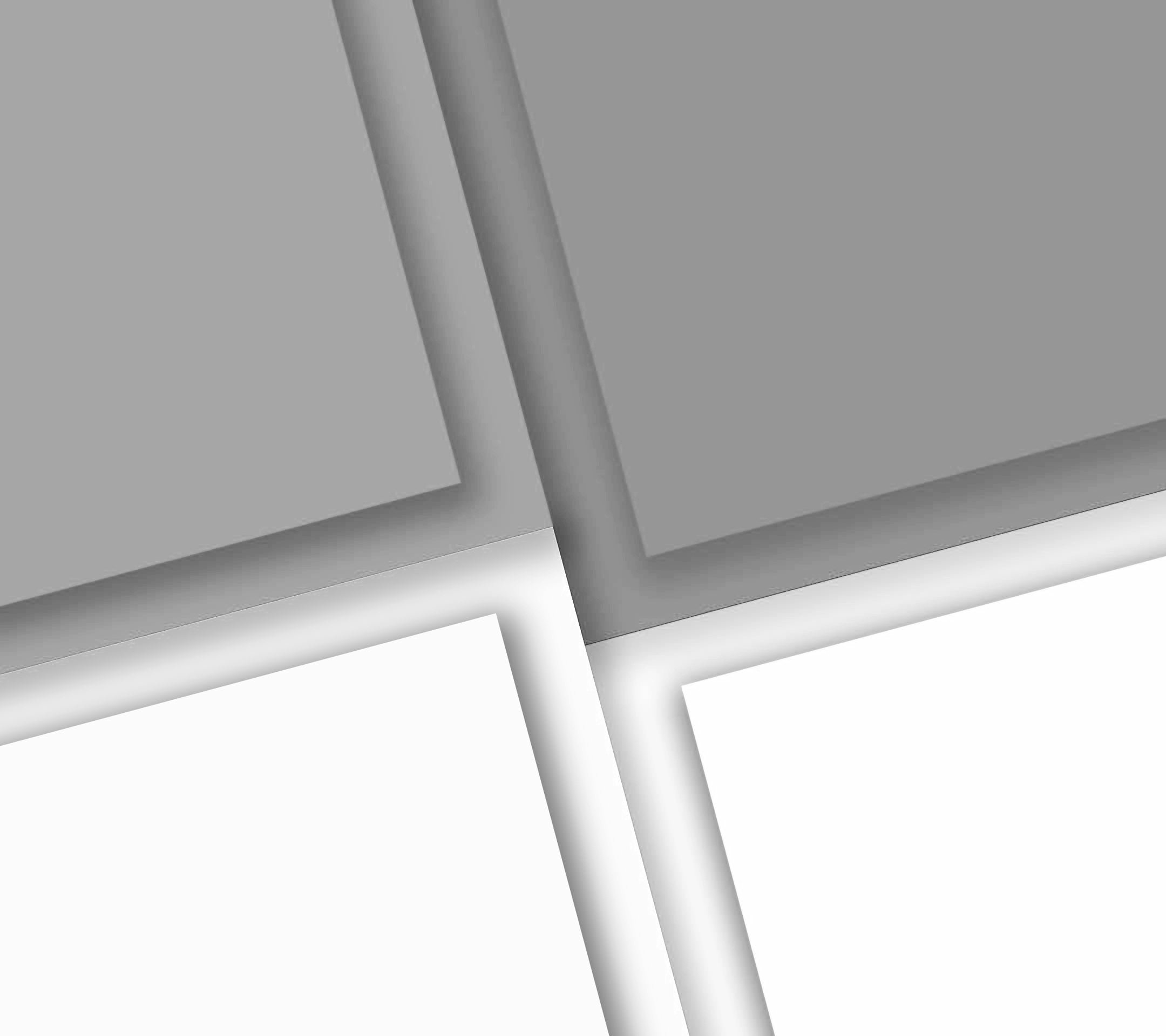
What are the risks and challenges associated with deploying a Machine Vision System?
Other articles on this site detail the benefits and advantages available by integrating and investing in machine vision capability. There are of course risks and challenges. This article discusses these with the hope that a better understanding allows for mitigation for these risks.
High Initial Costs and ROI Uncertainty
The cost of a vision system differs widely depending on the complexity of what is to be achieved. This cost includes not only the hardware components such as camera, lens, computer but also the development and integration of the application. The nature of machine vision is such that this engineering work will be undertaken by a highly skilled company or individual. There will therefore be an initial investment which in many cases can be substantial. Small and medium sized businesses may find this upfront cost challenging.
There's a risk that the return on this investment may not be as high or as quick as anticipated, particularly if the system does not perform as expected or if additional, unexpected costs arise. Key to mitigating this risk is to have a very clear and detailed understanding, between the developer and the end user of the system, as to what the requirements are; i.e.how many variations of product is it to cope with? What are the manufacturing tolerances inherent in the process? How consistent is the finish and material of the product.
Expertise Gap
Building and maintaining a machine vision system demands a certain level of expertise. This includes not only the knowledge to select and configure the right hardware but also the ability to develop and fine-tune the complex algorithms that power the system. Finding personnel with the right skill set can be a significant challenge for companies, leading to a shortage of talent capable of managing and maintaining these sophisticated systems. It is critical that the end user ensures the support for the system is there over the medium and long term and that the handover of the completed system is such that, to the extent it is possible, it gives the end user autonomy with supporting the equipment. When selecting the supplier the end user should think it terms of a long term vision partner and not simply in terms of the initial development and deployment.
Integration with Existing Infrastructure
Many manufacturing environments operate with legacy systems that were not designed with machine vision in mind. Integrating new technology with existing infrastructure can be a complex task. Compatibility issues, software conflicts, and the need for additional hardware modifications may arise, leading to disruptions in the manufacturing process during the integration phase. Many vision applications will demand that products are presented in a regular fashion. A metal press, for example, may eject parts in an uncontrolled way which may result in critical features being obscured from the view of the camera. Planning is everything, if the issues are known they can addressed and catered for.
Environmental Variability
Manufacturing environments can be unpredictable, with fluctuations in lighting, temperature, and other environmental factors. Machine vision systems heavily reliant on visual data may struggle to adapt to these variations. Ensuring consistent and reliable performance across changing conditions is a difficulty that needs to be planned for. There are solutions to these challenges, it is of the utmost importance that these factors are understood and addressed at the project planning stage.
Maintenance and Downtime
Like any sophisticated technology, machine vision systems require regular maintenance to ensure optimal performance. Downtime during maintenance can be a significant concern for manufacturers, as it may interrupt production schedules and impact overall productivity. Establishing robust maintenance protocols and scheduling downtime strategically becomes crucial in mitigating these challenges.
Complexity of Calibration
Calibrating machine vision systems to perform accurately in specific manufacturing environments is a meticulous process. Achieving the right balance in calibration to account for variations in product sizes, colours, and other factors is a challenge. Incorrect calibration can lead to false positives or negatives during inspection, impacting the reliability of quality control processes.
Adaptability to Product Variability
In a manufacturing setting where product designs and specifications may change frequently, machine vision systems need to exhibit a high degree of adaptability. Ensuring that the system can seamlessly transition between different products and variations without compromising accuracy can be a complex task, particularly for industries with diverse product lines.
Training and Acceptance
Introducing machine vision into a manufacturing environment often requires a shift in the work culture. Employees need to be trained to understand, operate, and trust the technology. Resistance to change and the need for extensive training programs can slow down the adoption process, affecting the overall acceptance and effectiveness of machine vision systems.