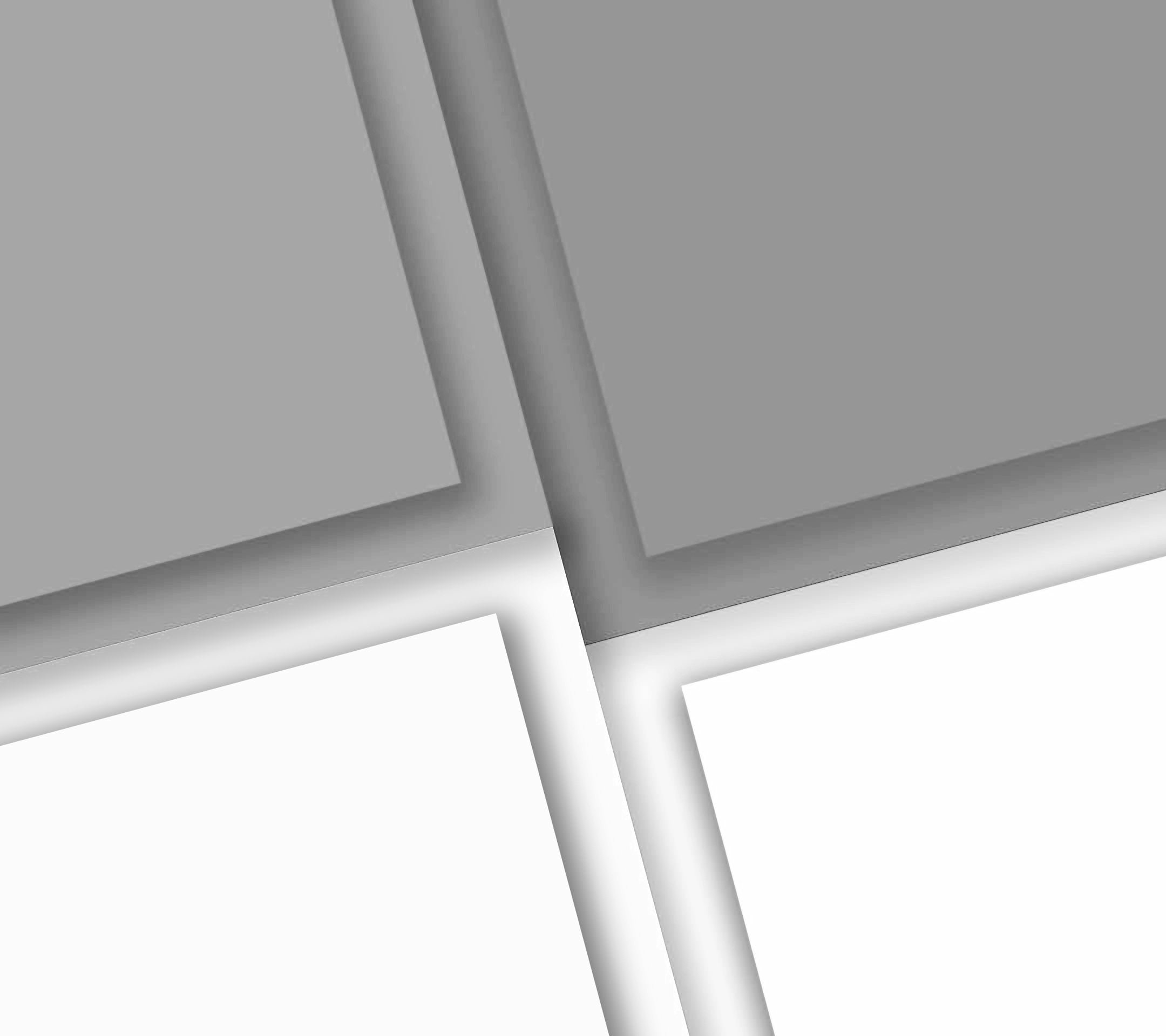
Case Study: Ball Bearing Verification
Automated Vision System for Ball Bearing Detection in Band-IT Ties
Manufacturing Process & Inspection Challenge
Band-IT (Staveley, Chesterfield) required a high-speed vision system to ensure quality control in their automated tie manufacturing process. The 3mm ball bearing, essential for correct tie function, needed to be accurately detected—despite limited visibility constraints.
The ties are produced in a fully automated machine that assembles a metal strap, buckle, and ball bearing. The process occurs at a speed of one tie per second, with components fed via bowl feeders and a continuous metal reel. Once the buckle is attached, the ball bearing is inserted, and the retaining tab is bent into place, the tie is ready for inspection.
The vision system had to be retrofitted into the existing machine to verify three critical features:
Presence of the buckle
Presence of the ball bearing
Correct bending of the retaining tab
Inspection had to occur at a specific stage—the last opportunity where the tie is fully formed yet still controlled by the machine, allowing for defective ties to be ejected. However, at this point, the tie side of the buckle faces the machine, making direct camera positioning impossible.
An assembly was designed and implemented to switch the optical path through 180°.
Optical Path Solution
To overcome the limited viewing angle, a mirror assembly was designed to redirect the optical path by 180° using two right-angled mirrors from Edmund Optics. These mirrors feature protected silver coatings, ensuring durability, oxidation resistance, and minimal light loss.
Lens: Fujifilm HF-XA-5M Series
Ensures consistent image sharpness across the entire frame, even with variations in focus or aperture.
Ideal for high-precision imaging in industrial environments.
Illumination: TPL Vision Diffuse Array
Compact form factor maximizes space efficiency.
High-intensity output & uniform lighting compensate for light loss through mirrors.
Short exposure time minimizes motion blur caused by vibration.
Camera & Processing: Cognex In-Sight 7600 Smart Camera
High resolution & high-speed image processing for rapid defect detection.
Robust industrial design ensures reliability in harsh environments.
Performance Monitoring & Verification
A custom PC interface provides real-time system monitoring, allowing operators to visualize performance. A built-in verification routine ensures system accuracy by allowing defective samples to be tested at the start of each day, with results automatically logged.
Conclusion
By integrating a high-precision vision system, Band-IT achieves 100% quality control in their automated production line. This solution enhances reliability, minimizes waste, and provides real-time defect detection, ensuring every tie meets strict performance standards.