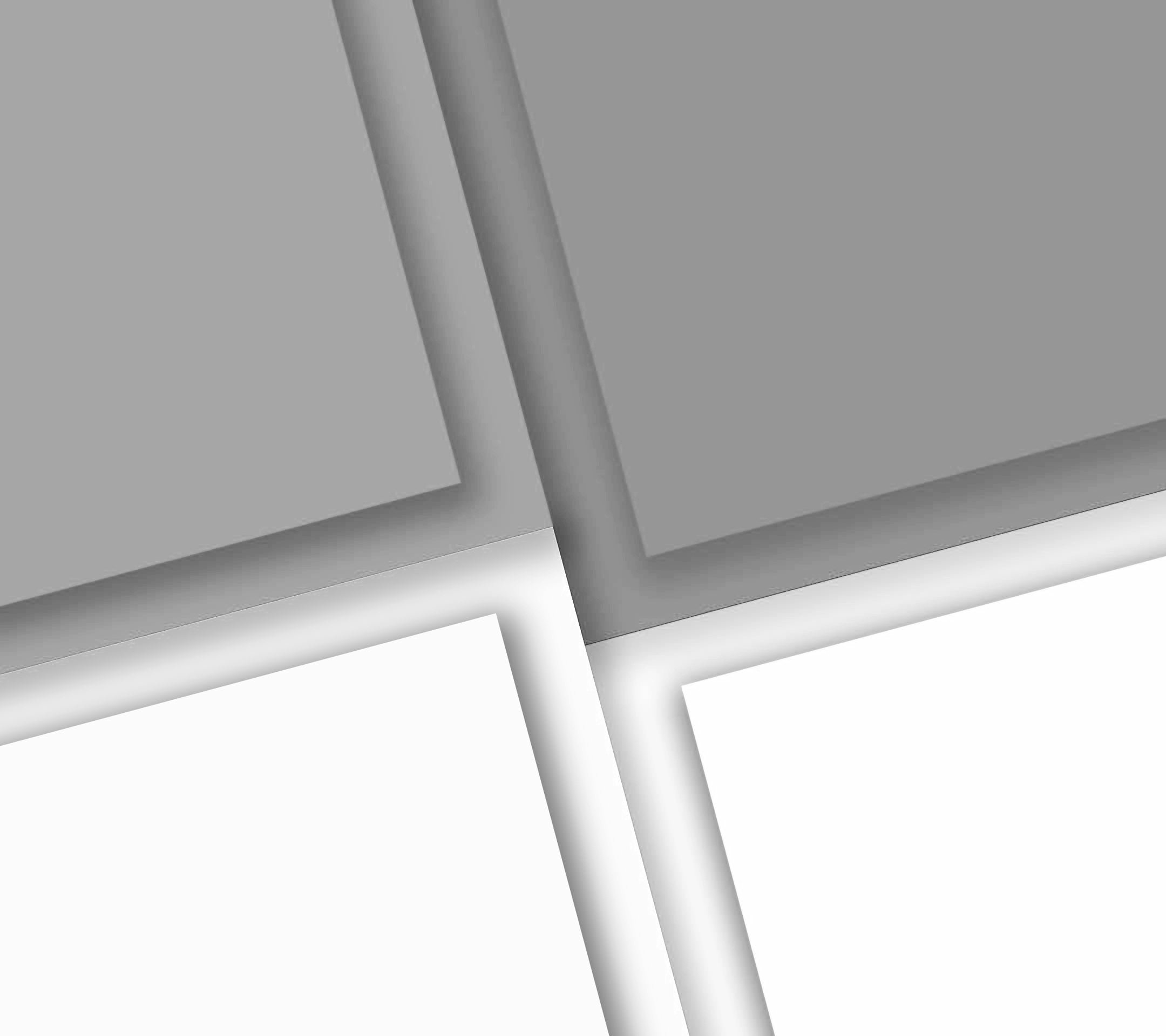
What is Machine Vision and how does it work?
Machine vision refers to the capability of a system to interpret, inspect, and analyse visual data. This technology enables computers to have an advanced, highly precise, and efficient form of visual interpretation, significantly surpassing human capabilities.
A vision system comprises both hardware and software components
Cameras and sensors are at the heart of a machine vision system. These cameras can range from standard resolution monochrome digital cameras, to more complex 3D imaging systems, this is dependent on the application. The camera captures visual information such as the shape, colour and size of an object. This image is then processed by the system. In environments like precision engineering, high resolution cameras are essential for capturing minute detail, 3D sensors may be used for capturing depth information of complex parts, or for looking for scratches or pits in a machined surface. The camera or sensor is selected depending on the requirements of the application.
Clearly, as the system will process and extract information from the acquired image, it is critical that the image is of the highest quality. Therefore the selection of appropriate lighting is essential.
Specifying the correct lighting is critical, some of the techniques available are shown above
Schematic of a Machine Vision system incorporating multiple cameras
Different types of lighting (e.g. backlights, structured light, or strobe lighting) are used based on the object's features and the required inspection type. In other words, the lighting is selected in order to ensure that relevant features are highlighted in the image and that insignificant features are reduced. Consistent and well-controlled lighting is essential. It ensures that the camera captures a clear, unambiguous image.
Optics play a role which is no less important than the camera and lighting. The lens affects how the camera views the object. The choice of lens affects the field of view, the focus distance and the depth of field, all of which are critical for accurate image capture. Depending on the particulars of the application, it may be appropriate to fit the lens with an optical filter, a polarising or colour filter for example.
Once an image is captured it is analysed using sophisticated software algorithms. These algorithms process the image to extract the necessary information. This process might involve identifying shapes, measuring distances, recognising patterns or detecting defects.
Advanced machine vision systems employ machine learning and artificial intelligence to improve decision making. These systems can learn from a set of trained data, thus improving their accuracy and versatility over time. Especially in complex or variable environments.
Together the hardware and software elements comprise a system. Correctly configured the system is capable of ensuring quality, guiding robots, monitoring a process and many other tasks. The tasks it takes on are those which, typically, cannot be performed by humans, either because the process is too fast, the detail being analysed is too small or the focus, and sustained attention to detail & application of repeatable criteria, is not feasible for a human to sustain.